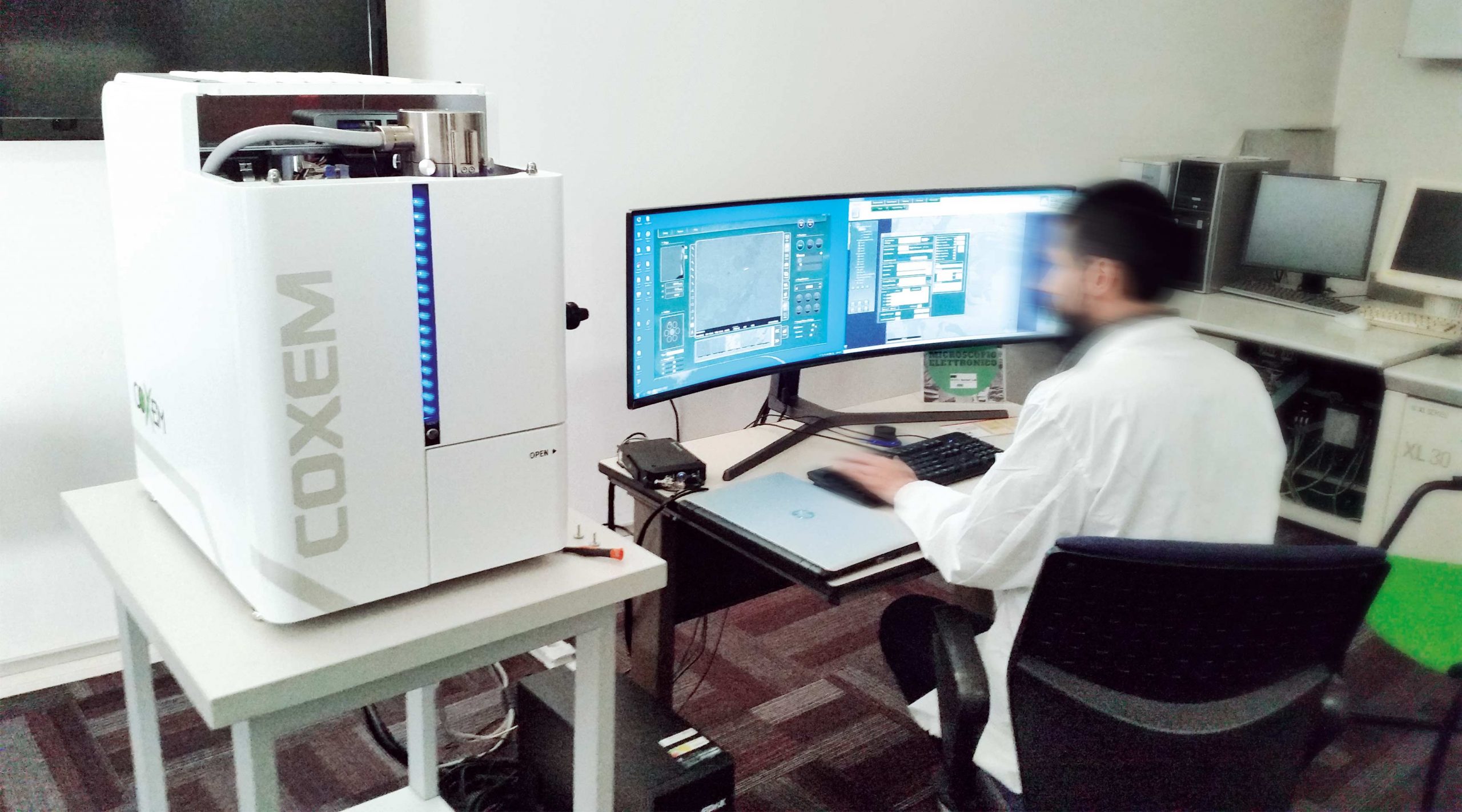
- POST-MORTEM ANALYSIS OF REFRACTORY MATERIALS
- REFRACTORY TESTING
- SCANNING ELECTRON MICROSCOPE
- GLASS DEFECT ANALYSIS
The refractory materials in a glass furnace have to resist not only extremely high temperatures, but also the corrosion coming from the glass melt and the furnace atmosphere. The post-mortem analysis of corroded refractory material after furnace service provides essential information about, and insights into, the correlation between furnace performance and furnace operation on the one hand, and refractory wear on the other. The interpretation of the microscopic observations makes it possible to explain the different corrosion mechanisms and, thus, provides valuable details and clues for a possible optimisation of future furnace performance and operation.
In order to simulate accelerated industrial working conditions and to predict the degradation of refractories, elaborate testing procedures are performed.
Corrosion
resistance
The
resistance
to thermal
and chemical
stresses is
tested with
the dynamic
finger test
and the
static plate
corrosion
test
according to
the
International
Commission
on Glass,
Technical
Committee 11
(the
so-called
TC11).
In the
dynamic
finger test,
a
cylindrical
sample is
rotated in a
platinum
crucible
together
with molten
glass. The
test is
carried out
with
predefined
parameters
(temperature,
time) and
the
reduction in
diameter at
fluxline
(three phase
contact) is
measured.
The
corrosion
rate can
also be
determined
by measuring
the decrease
in length
(forced
convection
at the
rotating
cylinder
face) as a
function of
time and at
various
rotation
rates.
In the
static plate
corrosion
test, sample
platelets
are immersed
into the
glass melt.
After the
chosen time
the fluxline
depth of the
corroded
samples is
measured.
This test is
carried out
with four
samples
under the
same test
conditions
and is,
therefore,
an
appropriate
method to
compare and
evaluate
certain
refractory
grades
together. An
international
round-robin
investigation
within the
Technical
Committee 11
of the
International
Commission
on Glass
confirmed
the good
reproducibility
of the
static plate
corrosion
test, and
the TC11
recommended
it as the
standard
corrosion
test.
Stone
formation
Due to the
interaction
of the glass
melt with
fused cast
AZS, solid
stones can
be
generated.
The defect
potential is
evaluated by
counting
this kind of
inclusion
inside the
remaining
glass after
each
corrosion
test.
Blistering
The tendency
of fused
cast AZS to
form bubbles
in contact
with molten
glass is
evaluated
with an
especially
developed
test
procedure in
which
standard
glass is
molten in a
fused cast
AZS
crucible.
The number
of bubbles
contained in
the glass
samples
after test
melting is
an
indication
of
blistering
potential.
The tendency
to release
bubbles is
expressed in
bubbles/gram
glass,
following
the
terminology
of glass
defects of
the
International
Commission
on Glass.
Exudation
In order to
evaluate the
expulsion of
glassy
phase, a
simulation
of the
load-free
preheating
stage, which
the
refractory
blocks in a
melting
furnace
undergo, is
performed by
heating the
test
material up
to
temperatures
comparable
to real
furnace
operation
conditions.
The test
procedure
follows the
recommendations
of the
Technical
Committee 11
of the
International
Commission
on Glass.
The
experimental
data of
REFEL
refractories
show that
for
temperatures
higher than
1500°C there
is only
limited
exudation
which
decreases
slowly with
service
time.
Vapour
attack
This test
method
according to
ASTM is
performed to
evaluate the
resistance
of
refractories
in glass
melting
furnace
superstructures
to vapour
attack. The
vapour test
method may
also be
useful for
evaluating
refractories
in other
applications
where vapour
attack
occurs.
The Scanning Electron Microscope (SEM) is used for the high resolution analysis of very fine crystalline structures as well as the analysis of glass chemistry and glass defects such as impurities and inclusions. Fragments of the material to be examined or ground sections – gold-vaporised surfaces for structure, carbon-vaporised surfaces for chemical composition – are scanned by an electron beam and displayed on a monitor for analysis. Due to the high degree of magnification, the special arrangement of the structure components and pores in the material under investigation become visible. It is, therefore, possible to qualitatively determine the existing elements during the investigation of impurities, and to make semi-quantitative statements on the chemical composition of the structure components of ground areas.
Glass defects
can arise
for various
reasons,
such as
unmolten raw
materials or
the
extensive
use of
recycled
glass
cullet, and
result in
the
occurrence
of unsightly
and partly
dangerous
inclusions.
Furthermore,
also melting
conditions
and their
influence on
the
refractory
materials in
the furnace
can
stimulate
glass
defects.
Through the
identification
of glass
defects
REFEL’s
experts can
give
comments and
recommendations
based on
their
long-term
experience
regarding
possible
causes as
well as
possible
preventive
or
corrective
measures to
avoid glass
defects in
the
future.
In doubtful
cases, the
results of
optical and
electron
microscopes
are verified
by X-ray
diffraction
analysis in
REFEL’s
state-of-the-art
laboratory.